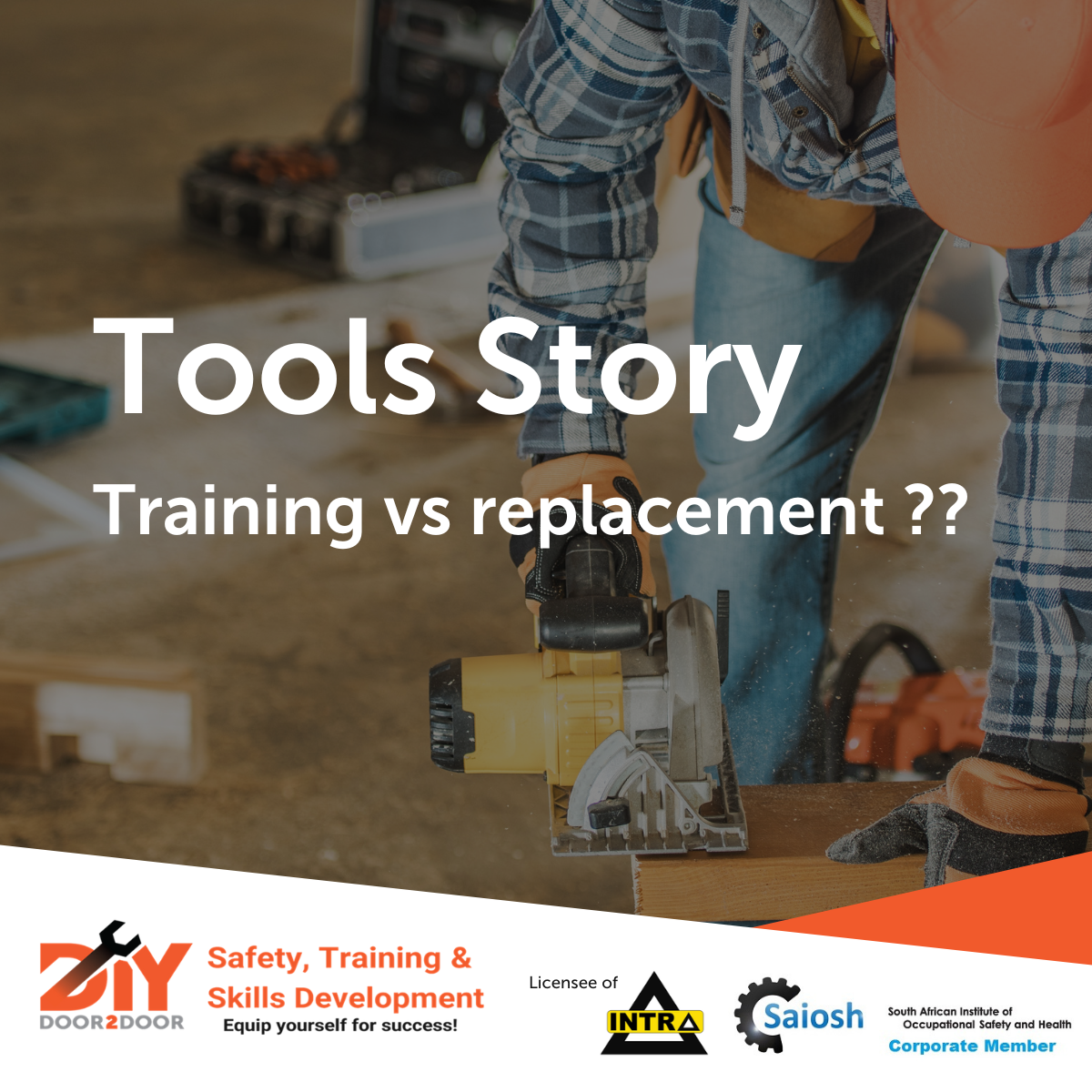
Hand & Power Tools Safety Training
Let’s start by saying, this is my observation on basic research undertaken over the past fifteen years and as yet undocumented. So, can I ask you the following question?
Would you spend money and time training your staff on the correct use of tools, machinery, or equipment they would use on a daily basis?
The answer that seems to be consistent throughout most industries that have had the question put to them is a resounding “NO”. Why would you want to spend money and time on training people who would inevitably leave you to progress to better jobs elsewhere at your cost? This is indeed a valid statement and in some cases the truth but let’s look at the value that is gained before we write this off as just another thing to spend money on. By training your staff you make them feel they are valued and are worthy of the cost of training, this helps build loyalty and a sense of pride in their achievements which can translate into better engagement and a feeling of ownership of their work and the tools of their trade.
Often the people using your company tools and equipment have never received any kind of instruction or training on how to properly use any of them. Let’s be honest who thinks training someone to correctly use a drill, a spanner or a hammer is a useful use of time, they should know how to use these everyday items right? Sadly, the truth is that many of the people being hired to do these types of work have, other than watching someone else use the equipment never been shown the correct way to use any of it.
The second most common response is “Well it's cheaper to replace the tools than pay for training and I cost it into my quotations”. This too is a perfectly valid response until you look further into the statement and start to look at the actual numbers (I could at this point go into the figures and numbers but as I have said before this is based on my observations and experience and I am sure there would be numbers to support both arguments) so I will try to keep it as simple as possible.
The replacement of tools and equipment is not as simple as adding the replacement cost of saying a power tool or a lifting rig to your next quote as you are sure at some point it will be broken or stolen, sound familiar? I have said it myself a number of times. There as so many other hidden costs to take into consideration, the downtime while waiting for the new item to be purchased or delivered (let's be honest, who actually buys these things when the contract is awarded). With the ever-increasing cost of the actual products being replaced, in many cases, the cost will have risen significantly since the original quote was done. If the tool or equipment is not being used as intended the new one may only last a very short time and manufacturers or suppliers will not warrantee goods that have been damaged through “misuse” or “negligence”. The end result is that the replacements that the customer is paying for actually end up costing the business way more than they have allowed for. With our economy being constantly under pressure and competition for work higher than ever often these costs are left off in order to remain competitive.
Is training worth it? Well, that remains an interesting question to which there may be no simple answer. I do believe that the cost of training employees will be greatly offset by the benefits of being able to hold them accountable for the tools and equipment in their care. Better training has been shown to lead to better care and proper use of these tools and equipment which extends the lifespan and drastically reduces the need to replace them. Part of the training process also helps employees identify risks and bring them to the employer’s attention which further assists in keeping the equipment in working order and the employees further engaged.
The final decision is completely up to each business or individual as to which direction they will choose if any. There may not be a right answer but, is it not worth looking at investing in our people and letting them be part of the solution, or do we just replace the equipment and/or the people?